Geothermal heating and cooling systems, also known as GeoExchange or Ground source systems, tap into the captured solar energy stored below the surface of the earth, to offer exceptional comfort conditioning for commercial buildings. “Geothermal” pertains to the heat of the earth, which contains a vast reservoir of low-temperature thermal energy – typically 10 times that required over an entire heating season. This resource is free and constantly re-supplied by the sun. A geothermal system captures this free energy from the earth by using water pumped through a series of pipes (an earth loop) buried in the ground. Highly efficient geothermal systems use a small amount of electricity to capture and move a large amount of free energy.
The water to water heat pumps are single packaged heating/cooling units, that have the ability to be cascaded to meet any building load requirement. The water to water heat pump units, are designed to operate with source liquid temperatures between -1.1°C and 38°C and is capable of providing heating or cooling across the range -1oC to 65oC, dependant on the building requirement and application.
All heat pump units contain sealed refrigerant circuits, each containing either hermetically sealed scroll or screw type compressors, electronic expansion valve assembly, brazed plate or shell and tube heat exchangers, factory installed high and low pressure safety switches, freeze protection, service ports, and liquid line filter driers. Compressors are designed for heat pump duty with internal isolation and are mounted on rubber vibration isolators.
The compressor motors have internal overload protection and dedicated power speed drives to increase efficiency and reduce noise on startup.
Due to the location of certain plant rooms and locality of high level offices, additional vibration isolation can be incorporated within the manufacture of the heat pumps to minimise, as best is practicable, the effects of impact and airborne acoustic transmission through the building. This can include;
- Additional insulation on panel walls which significantly attenuates sound level.
- Three tier impact vibration isolation on compressor mounting.
- Flexible suction and discharge connections to further dampen vibration transmission through the unit pipe work.
With the above inclusions incorporated very low environmental impacts can be achieved. A tested maximum result of 46dB(A) during 60RPS and 90 RPS compressor conditions (see below).
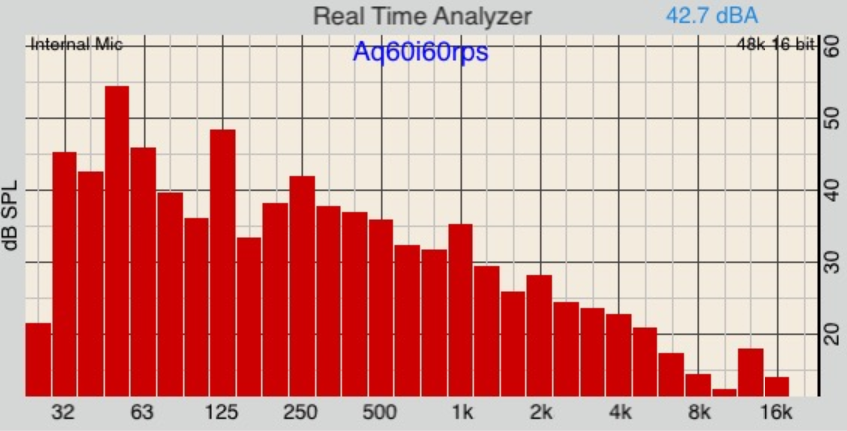
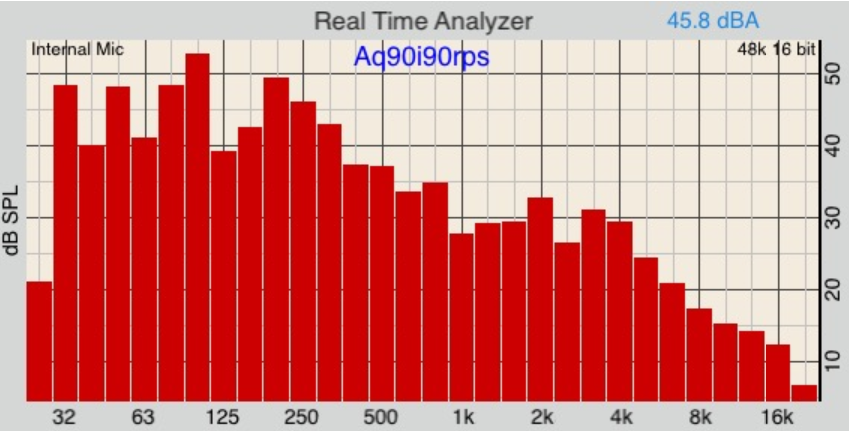
Controls and safety devices are factory wired and mounted within the unit.
Controls shall include 24VDC activated compressor inverter drives, transformer with built in circuit breaker, and anti-short cycle protection.
All the heat pump units will be supplied with a network interface card which will permit the heat pump units to be connected to our proprietary primary energy centre controller management system.